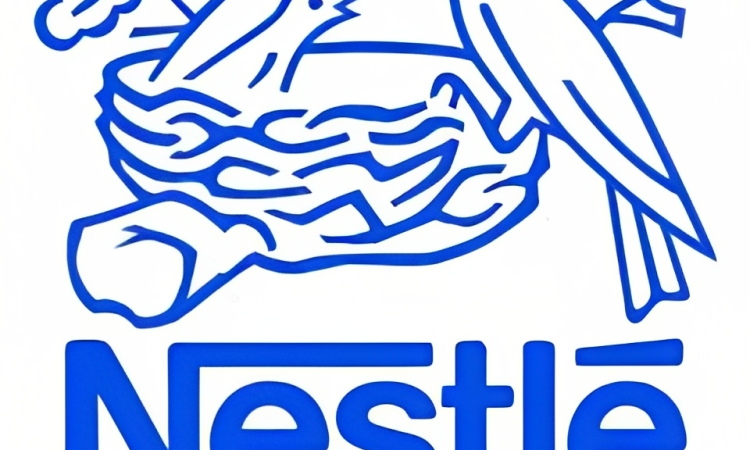
Nestle Nigeria Plc – As the Leading Nutrition Health and Wellness Company, we are committed to enhancing People’s lives, everywhere, every day. Infact enhancing lives will influence everything we do together.
A presence in more than 130 countries and factories in more than 80 research centres brings many global benefits. We believe in long term career development and appreciate how challenges and motivation will help you reach your potential. Nestle Nigeria Plc upholds the principle of Non- Discrimination and Equal Employment Opportunities in its recruitment processes.
We are recruiting to fill the position below:
Job Title: Factory Costing Specialist
Location: Sagamu, Ogun
Position Type: Full-Time
Job Summary
- Joining Nestlé means you are joining the largest Food and Beverage company in the world. At our very core, we are a human company driven by our purpose to improve the quality of life and contribute to a healthier future.
- Nestlé Nigeria is currently looking to fill the position of a Factory Costing Specialist, whose responsibilities include to support the Factory in the pursuit of cost optimization and compliance at the factory by providing visibility and insight into manufacturing variances.
- This will include the suggestion of corrective actions based on sound knowledge of manufacturing processes and cost drivers.
- Develop his/her financial and technical skills and interacts with cross-functional teams throughout the organization.
- The specialist exercises good judgment stays focused on results and ensures the integrity of financial reporting in a fast-paced dynamic environment.
Requirements
A day in the life of a Factory Costing Specialist:
- Cost Control and Management will done Daily
Perform well robust health check:
Cost center check
- Timely detection and correction of wrong posting (GL & CC)
- Putting measures in place to ensure right posting from source
- Ensure all CCs have the right activities
- Monitor evolution of expenses to promptly identify unusual occurrence
Material Ledger
- Monitor price evolution trend and provide its impacts on COP
- Ensure PO conditions are correctly maintained
- Ensure correct FIFO valuation
Controlling
- GR spot check and tracking
- Material usage and Teco of PO review
- Ad hoc investigation and reconciliation
- Review and analyze actual Costs of Production (identify key drivers, provide analysis and explanation on results, provide insight on trends)
Weekly
- Material usage variance – Manufacturing with detail understanding of deviation
- Coordinate random stock count
- Ad hoc analysis and simulation
- Working with AG for BOM update and cleansing
Reporting:
- Automation of key routine activities
- TDC saving tracking
- Conversion cost analysis report
- Drive monthly Variance Report
- Prompt expenses control report for Engineering and Production
- Master Data: factory health checks and give inputs for the revision of Service Level Agreement according to new reality
Internal Control and Compliance:
- Establish control measures to ensure transparency in the following areas:
- Technical store and consumable
- Engineering general services
- Production and Engineering departments
- Establishment of systematic review and reconciliation of contract related payments
- Ensure full compliance with external regulatory requirements through prompt follow up of renewal of licenses, permits, etc.
- Follow costing guidelines and associated standard operating procedures when generating financial documents and performing daily activities.
- Coordinate and Ensure Stock Taking are periodically taking place & Write-Offs are duly authorized to avoid misappropriation of goods and company assets
- Perform routine audit activities within the factory to ensure compliance on critical areas, e.g. stock taking. Appropriately escalate business risks.
Fixed Assets and Project Management:
- Liaising with project team to ensure timely completion of AUC items.
- Generating and analyzing AUC components and follow up for completion in timely manner
- Work with Project team to determine the correct value for capitalization
- Ensure prompt capitalization once the asset have been put into use in line with NAS
- ACE depreciation calculation considering existing assets, AUC and projected credits
- Monthly review of the year depreciation projection to be reflected in DF submission
- Review the existing procedure for asset verification and tagging
- Put in place rolling plan for asset physical verification and tagging
- Provide comprehensive verification report for management review and approval
- Review the existing procedure for asset scrapping and disposal
- Follow up for E2E completion asset scrapping and disposal
- Update the asset register accordingly on a timely manner at a regular interval basis scrapping and disposal.
Business Planning:
- Coordinate and provide Plant inputs for factory cost budgeting, capacity runs, planning and for the dynamic forecast. This requires continuous involvement and awareness of current situation to discern feasibility of inputs.
- Active participation in Standard Cost Budget, Revision and Replacement Cost calculations as required.
Cash Flow & Continuous Improvement:
- Seek and support cost improvement opportunities, be an active contributor to improvement projects and initiatives.
- Participate on project teams to ensure validation, review and proposed savings are accurately tracked.
- Involved in daily activities associated with NCE in the factory environment.
Knowledge Transfer:
- Prepare and publish financial KPI data on a regular basis; perform analysis of KPI data and transfer this knowledge of the key figures to the relevant stakeholders to promote understanding.
Co-Piloting Role:
Provide supports to Factory E2E operations:
- Good materials reception and consumptions of key items (especially technical consumables)
- Compliance and audit processes
- Training of personnel in best practices in relation to administrative control
- Liaising with Manufacturing excellent in driving projects.
What Will Make You Successful?
- HND / B.Sc. in Finance / Accounting
- Professional Qualification such as ACA, ACCA or CIMA is required.
- Minimum 3 – 5 years of prior experience in Costing or Accounting, ideally within a factory or supply chain function of a manufacturing company.
What we Offer
- Interesting and challenging work in an international company – a branch of worldwide and well recognized FMCG concern
- Possibility to work in a dynamic team of professionals and leaders
- Possibility to work with challenging projects and responsible tasks
- Atmosphere full of respect, professionalism, and excitement
- Possibility of development & career advancement
Application Closing Date
Not Specified.
How to Apply
Interested and qualified candidates should:
Click here to apply online